Here at Encore, we find ourselves problem solving daily, but this job we had to label as a Pre-Cast Epic. This job was a journey that started with a lot of planning, incurred many on-site tweaks, and ended with acquiring a very solid client. We were also able to make the Site General very happy, and in doing so we cemented a relationship with one of the largest construction fabrication and erection companies in Canada. This was done using our specialty cranes and problem-solving skills.
The Planning Stage
It started when we were asked to check a job on one the University Campuses here in Edmonton, AB. The location to scope out was at a shipping entrance to one of the older building. This campus is a maze of twisting back alleys and streets with beautiful trees overhead. We met with the steel crew on site and began our discussions. What we saw was a wide-angle ram that led down to a shipping / receiving area. Several Pre-Cast walls were being installed from the top of the ramp down to the bottom. From a first glance, it didn’t look like a big deal as the angle was only a little more that we would have liked. The weights were within reason and well within our crane charts, about 12,000 – 15,000 lbs (5,400 – 6,800 kgs).
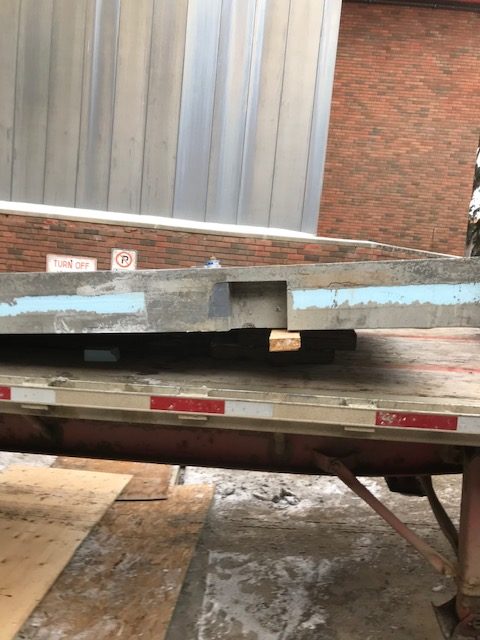
The final three walls we had to maneuver through consisted of two tall ones and then an overhead arch span, which were all under the mezzanine. The outside concrete wall dropped down from the second story. We realized that there would be a decorative touch to this move, as were left with only 10 ft clearance from the concrete floor. Once under the wall, the interior roof was just over 12 ft high. We would have to get the slabs under the overhang, and they were 12 ft high and just over 8000 lbs (3,600 kgs).
Our job was to get the under the overhang, then stand them up and put them into place (which was a very tight fit). We knew that no ordinary crane was going to do this lift. Luckily we had a special jib on one of our larger knuckle trucks that I knew could reach under and still lift a load like that up and into place. Since the wall was on one side of the shipping dock, the crane would have to be on the other and reach across. Our measurement looked like a 40 ft plus reach, and the crane chart said it could handle that weight.
My first concern was the ramp. My crane would have to sit on the ramp and because of the angle, that would push the height of the crane up. We were already starting at 12 ft, but as we worked our way up the ramp, we would be at 13 ft, then 13.5 ft, then 14 ft and increasing. That is a concern, as we are going under and then up. I had to confer with my operators, as they would tell me straight. We all agreed that this one was a pickle, for sure.
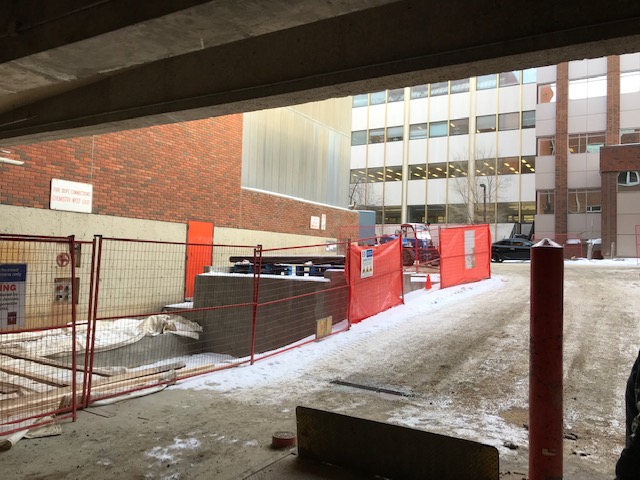
Later I went to the Pre-Cast yard to first-hand inspect the slabs themselves as I needed to know how they had designed the lift holes. I needed to see if they had a plan… they didn’t. I found the stored slabs, checked the numbers against the design plans I had. The only lift spots on the interior panels were on the very top, and these two were being placed within an inch of the roof. So, I went and met with the Head Guy of the Pre-Cast yard and told him about the lift. He laughed, which is not a good sign. He then tells me they turned that job down because it was an impossible fit. I though, “Okay, real funny.” All this effort so far and the supplier doesn’t want to supply.
So, I went back and had some more serious conversations about solutions. I suggested that we could build a lift frame and squeeze around the Pre-Cast, then we could ratchet the whole thing together, and lift from a solid point about a third from the top. We could use a solid swivel, one that we had worked with before and trusted. This would be an engineered device, which is kind of a big deal to fabricate for only two lifts.
The other way would be to drill a hole in the slab and put a bolt through it. The problem is that slabs a finicky, and I didn’t want to break one. I called the steel crew and gave them the good news and the options. We had some time before the job was scheduled, so we let everything simmer. We gave our customer some tough decisions to make. Based on our expertise and experience, all we could do was let that settle in their minds and let everything calm down.
Discussions with all team members
A couple days later I bumped into the Pre-Cast crew of the supplier. As we know these boys quite well, I ran it by them as it’s nice to get a real, experienced voice on the problem. Their main man, Blaine, thought the swivel and bolt arrangement through a 1 1/4″ hole through the slab would work. I had a couple of sizes of these heavy-duty swivels that could rotate to any angle and pick it up safely, and they could also be fitted with various sizes of bolts, so we had an answer to our solution.
I still needed more answers on the slabs, so I went back to have a closer look at them. They were concrete slabs on the outside, but on the inside, they were loaded with insulation. They were also thicker than I thought, about 8″, not 6″, and they looked solid. We were able to get the holes drilled dead centre, 4 ft from the top. I was advised to drill 3 ft, but I kept looking at the overhang drop that we had to get under, and since the reach distance and the ramp the truck had to sit on, I confidently went with 4 ft and drilled the holes. Our measurements told us the crane would be 40 ft (+/- a couple ft) away, and that was pushing my load chart to the 8,000 lbs capacity.
To add one more layer of difficulty to the cake, there were two bollards, 6″ in diameter, placed in the alley to block any vehicles from backing under the mezzanine. I asked the steel crew to remove them, which was a good call in the end. The jib that we needed to use was just shaped like a curved hockey stick, which makes it possible to change the angles and lengths, but it can be an awkward beast when you try to get close to the actions.
The Big Day
As erection day loomed, we planted trailers in the Pre-Cast yard and the way in was bit of a driving test. We had to use the shortest possible trailers we could, 31 – 35 ft long. The shipping crew told us that we needed three separate trailers because of the way the slabs needed to be transported. Some needed to be horizontal, while others were cradled on their side in “A” frames. The outside wall erection was like another job completely. We needed a different crane; a big straight boom. One with two winch lines and two swivels complete with a sliding cable rig up in order to lift the walls off the trailer, and then orient them for placement. That part was easy.
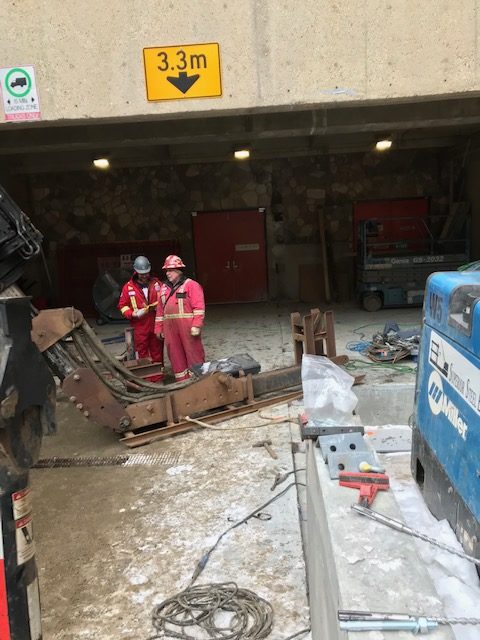
The interior work, on the other hand, that was a headache. We were worried that our reverse knuckle would need help lifting, or just getting the pieces under the overhang. We substituted a short, day cab picker truck for the tractor which allowed us to pull the little trailer down to the access point and help out if needed. A I mentioned before, this campus was a labyrinth, and our site was buried in it. I created maps so that my team could find it and we planned our routes in.
We would be going around buildings, under walkways, and in-between alleys. Finally, we’d make a turning point and back around two curves through a gate to jack-knife the trailer into position. It sounds hard, but when you surround yourself with professionals, they make it look like the Oilers winning the cup in ’88. The first day the trailer squeezed in tight, on level ground, just off to the side of the ramp. Our operator, Fred, set-up on the opposite side at the bottom of the ramp and had a good line of sight from his crane. He was under the wall, which gave him clean access to the final slab location.
We were fortunate that the first walls, which were shipped laying horizontal, had the correct face showing, but we still had to lift them to fit our plate and bolt system. Our picker tractor raised them high enough to insert the first swivel bolt package… so far so good. Fred then swung our reverse job over to hook it in and lift it up, but the job was angled so high (it had to be), that the elbow contacted the slab before we could hook up.
We used the other crane again, this time to stand the wall straight up. It was a lot of effort for the little 18 ton, but she lifted the slab in confidence. We then had to be careful not to drag it and chip the concrete. We were able to lift it, and we set it off to the side of the trailer. The wall was then stabilized, and Fred was able to attach the swivel to his hook.
Now we were underway. The wall swung to the overhang, looking big and heavy, but our rig was solid and the concrete in the wall was showing no signs of strain or cracks. The first wall hung fair and straight. Placing three tag lines to the bottom of the slab, we approached the overhang and got members of both crews to pull on the lines, as we were trying to gain enough of an angle to raise the bottom and get under the overhang.
We could barely budge this slab. Fred was ready and had his Come-Along in his bag of tricks. We secured it to the boom off of a lift point, and selected the proper length of sling, and pulled the concrete wall back until we had enough angle and enough height. Fred the swung the wall smoothly under the overhang and started to lift the load into the now available interior headroom. The jib allowed him to lift right to the ceiling, and as he did, we slowly released the Come-Along and let the slab return to near vertical.
The clearances were so tight that we needed to keep a bit of angle until we were at the final installation spot. Fred then maneuvered the wall closer and further in, but the wall was heavier than we thought. We were still 6 – 8 ft from final touch point, and the crane was reaching its limit. We had to switch modes in order to slow down the crane functions and add 10% more lifting capacity to its chart. It still wasn’t enough and now we found ourselves in a pickle.
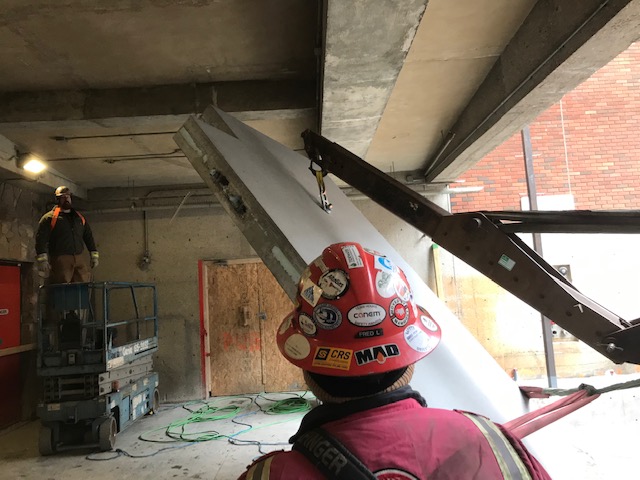
Catching our breath
We had to pull the wall back to a better position for our charts, and we took a moment to catch our breathes. At this point, we had to tell the crew what was happening. Ultimately it is their job site, and they deserve to know the bad with the good. In our experience, you need to accept help when it is offered, and you can never be too worried about honestly explaining a situation. I was thinking, “What happened to my measurements? What happened to my chart readings?”
We checked the crane positions again, and we were slightly further over than our initial plan. I then noticed we didn’t take advantage of the space allotted to us from removing the bollards. We had one problem though; there was an 8,000 lb plus slab in the air! The roof structure above us was not perfectly flat, and there were protruding, concrete partitions hanging down a foot or two.
We had another site meeting with the erection crew, who were starting to get impatient with this tedious process of rigging and setting up. When you work with Iron Workers, you’re working with the best and toughest crews on site. Just don’t get in their way. We moved our wall and braced it against the overhang. It stood like a rock, and we managed to tie it to a friendly column.
Fred cut loose and we moved the crane over and deeper into the site. I was worried that we were now so close the Fred wouldn’t be able to move his jib back under the overhang. The Master Crane Operator got under it with 4″ to spare. We hooked back into the swivel, lifted the big, slender girl and set it right into place. The hard part was over, but the rest of the work wasn’t necessarily easy. Fred confidently did his thing and placed all three walls in one day. Our 50-ton straight boom finished the exterior walls the next day.
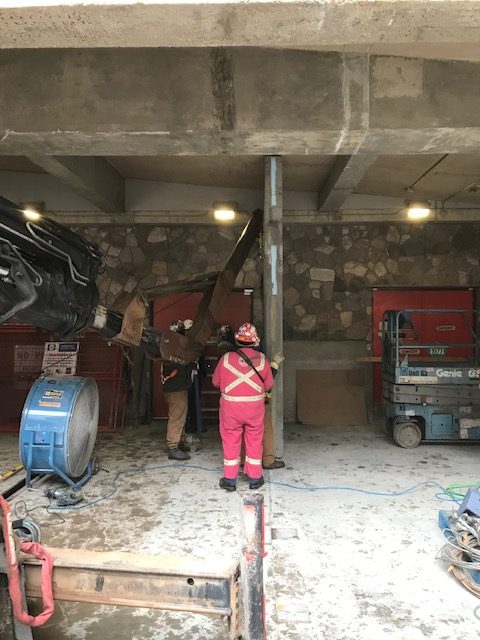
Our client had quoted this job for 4 days, and with our expertise, it was completed in only 2. We were able to solve their problem safely and effectively, and we all walked away with a little more knowledge, expertise, and money. As you can imagine, it could easily have taken 3 or 4 days. We did it in one.
Don Lucas, Owner Encore Trucking & Transport